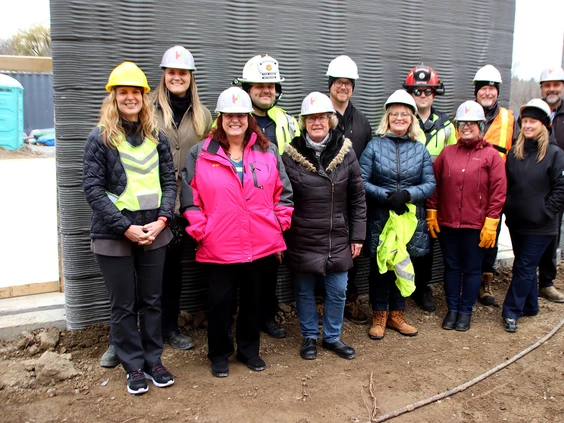
Construction begins on 3D-printed buildings in Gananoque
By Lorraine Payette • For Postmedia Network
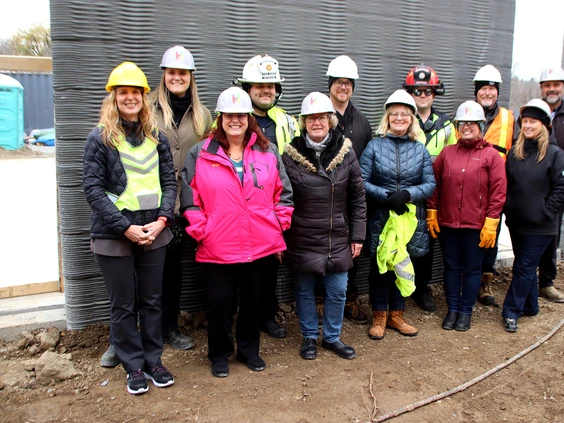
Construction began on the 3D-printed buildings, which were approved by Gananoque’s council under Mayor Ted Lojko on March 2, 2022. Designed and planned by the Horizon Legacy Group (HLG), the project is using new construction technologies to create environmentally friendly affordable housing. The firm is based in Toronto and has a 70-year history in the field of real estate development.
“Since May 2024, the Gananoque project has made significant progress as Canada’s largest housing initiative to integrate on-site robotics,” said Claire Belerique, marketing manager for HLG. “The development, featuring 26 stacked townhouse units with 30 per cent designated as affordable rentals, is a groundbreaking proof of concept for how advanced technologies can tackle Canada’s housing crisis and labour shortages. It also represents a meaningful step toward providing an affordable housing solution for the local community, offering greater accessibility to quality housing.”
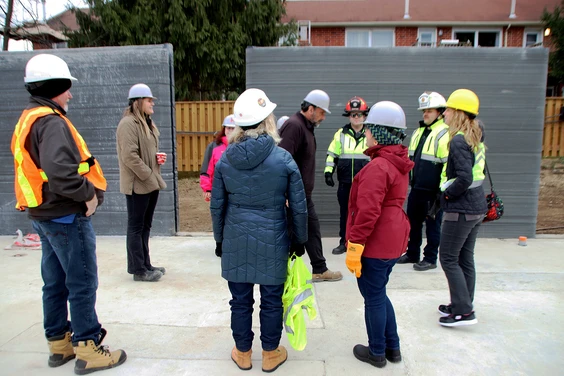
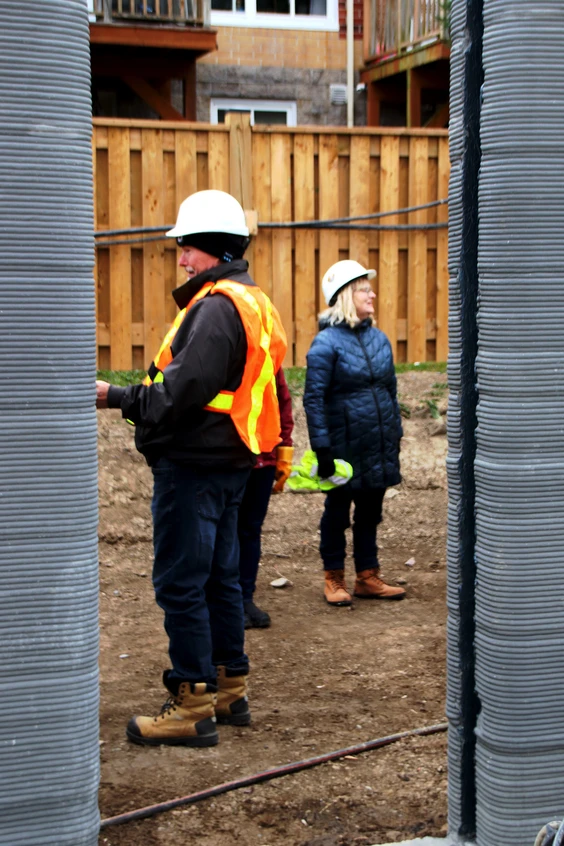
On November 14, dignitaries representing Gananoque Town Council, affordable housing interests, construction firms, the Gananoque Fire Department and others were invited to the site to see the project up close. An informational tour, led by Frank and Claire Belerique of HLG, allowed them to see what had been accomplished so far, and to watch Val 2.0, the construction robot, in action.
Using a special mix of concrete, Val extruded the material in uniform bands moving in a predetermined spiral. Starting at ground level and moving up one round at a time, it was able to quickly raise a wall, producing both interior and exterior surfaces at the same time, each having its own unique texture. The walls are hollow allowing for the addition of a drainage layer and spray foam insulation to maximize the R value while keeping costs under control. Spaces are left in the walls for the placement of doors and windows. The floor is a poured concrete slab, and only the first floor is robot-produced. Additional construction above that layer uses traditional techniques. A wall-tower section can be produced in about 3 hours using the robot.
“The robotics portion of the project is now complete, with Val, our construction robot, having automated repetitive tasks to improve efficiency, precision, and safety,” said Claire Belerique. “This milestone demonstrates how robotics can provide a scalable, turnkey solution for modernizing construction processes and addressing workforce challenges.
“We anticipate completing the project in Fall 2025. Over the past several months, the site has welcomed government leaders and housing experts from across the province who have come to see the project in action. Their visits highlight the growing recognition of how robotics and advanced construction technologies can transform the industry and meet critical housing needs.”
The complex is being constructed on Fourth Street in Gananoque on a two-acre lot.
“We’re only using approximately half of the lot for the construction the other half we plan on doing some community gardens and some sort of landscaping elements,” said Frank Belerique. “We have a 70-year history of building infrastructure and commercial real estate – office towers mostly – and we’ve also done some residential and some student. We were prepared to look at anything that would help speed up the construction process and looking for a way to create more affordable quality housing and we ended up with 3D concrete printing.”
There will be 34 parking spaces at the front of the building, with plenty of space left over for the landscaping projects.
“Horizon Legacy is committed to excellence in all we do,” according to its website horizonlegacy.com. “Our focus on quality, timeliness, and high standards has built a trusted brand. Our expert team ensures that our work makes a meaningful impact, enhancing communities and improving society.”

The project began as a dream of creating quality affordable housing while maintaining a minimal environmental impact. Buildings needed to be attractive and functional while producing as few carbon emissions as possible, climatically appropriate (warm in winter, cool in summer) without overstressing the grid or other systems, and able to withstand any weather and other stresses expected in the local environment. Keeping the costs of labour and materials under control while creating a product of maximum quality meant exploring and experimenting with the latest technology.
This article originally appeared in https://www.gananoquereporter.com/news/construction-begins-on-3d-printed-buildings-in-gananoque